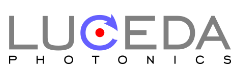
IPKISS AWG Designer
Overview
The IPKISS AWG Designer is an IPKISS module that provides an integrated design environment to design Arrayed Waveguide Gratings (AWGs) from high-level specifications to manufacturable AWG layouts, offering expertise, assistance and control across all design stages:
- AWG high-level specifications
- AWG physical synthesis
- Simulation and verification
- DRC-clean layout generation
The IPKISS AWG Designer allows optimization across all stages of the design flow while having a press-the-button flow to a manufacturable layout. Each step of the process can be customized to suit specific requirements in terms of layout or simulation. The final AWG design can be used within the IPKISS Photonics Design Platform to complete the chip design and prepare for tape-out.
KEY FEATURES
Specification-driven workflow
Input
- Functional specifications: center frequency, number of channels, channel spacing, free spectral range, …
- Physical specifications that impact the optical performance (e.g. minimum spacing of the output waveguides)
- PDK and fab rules
- Material and model parameters (refractive indices of the materials used in the slab, waveguide effective and group indices, ...)
Output
- Finished AWG
- Reusable layout in IPKISS (compatible with IPKISS Link for Siemens EDA)
- Reusable circuit model in IPKISS
Customization
Aperture type
- MMI aperture
- Simple aperture
- Define and simulate custom apertures
AWG configuration
- Waveguide array (rectangular, S-shaped, freeform, ...)
- Waveguides
- Waveguide cross-section (layout, model, ...)
- Expanded waveguides in straight sections
- Rounding algorithms
Star couplers
- Output aperture spacing
- Number of grating arms
- Star coupler grating period
- Number of dummy apertures
- Contour drawing largely customizable to create DRC-clean designs
Simulation
- Field propagation simulations using CAMFR in the apertures
- Field propagation simulations in the free propagation region (Rayleigh-Sommerfeld)
- Analysis
- Insertion loss
- Transmission peaks
- Crosstalk
- Nearest-neighbor crosstalk
Tape-out and fabrication
- DRC-clean layout with IPKISS layout functionalities
- Full control over the aperture and star coupler drawing to match any foundry
- Silicon-on-insulator (SOI) and silicon nitride (SiN)
- Indium Phosphide (InP) and other material systems on demand
Supported IPKISS PDKs
- AMF, Tower Semiconductor, Ligentec, imec BioPIX, CompoundTek
- AWG support for other IPKISS PDKs can be added upon request
Support & Services
- Expert design support
- Customization services available
Master the key design parameters
The AWG resembles a lens-based imaging system: the field profile of the input aperture is projected by a 'lens' (the apertures and the waveguides) onto the output aperture. The waveguides act as a prism that is inserted between the lenses. It is not a perfect imaging system, because the waveguide array partitions the field into discrete 'pixels'.
Arrayed Waveguide gratings are most commonly used as wavelength (de)multiplexers: light with many wavelength channels comes in, and the wavelength channels are sepatared into different output waveguides.
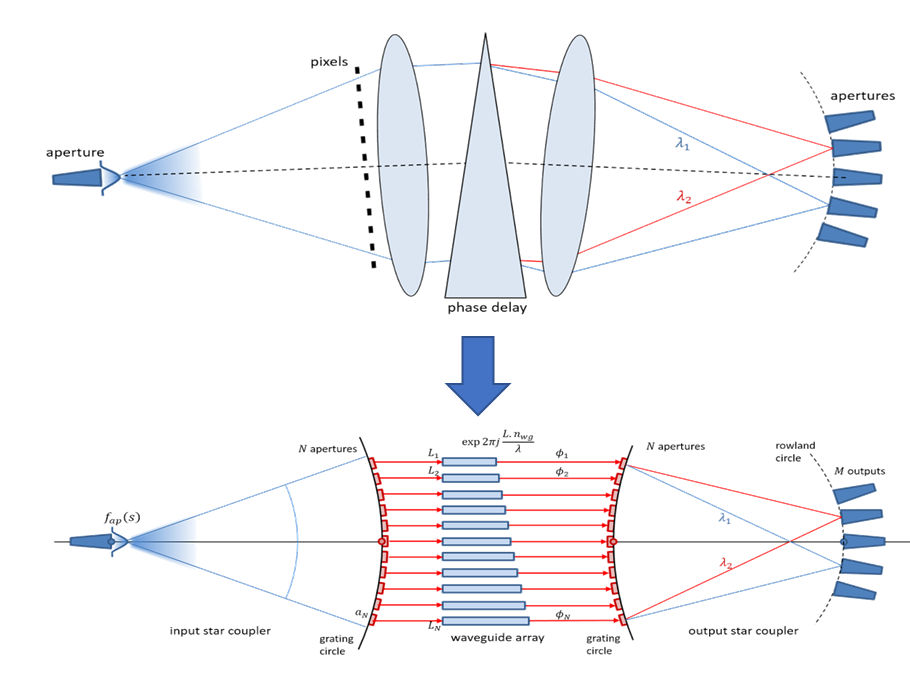
Design specifications
The important criteria for designing a demultiplexer are:
- FSR
- Center Frequency
- Channel Spacing
- Number of Channels
- Apertures
- Waveguides
- Free Propagation Region
- Number of grating arms
Performance metrics
The important metrics in the performance of an AWG demultiplexer are
- Insertion loss of the channels (i.e. how much light is coupled to the correct output)
- Crosstalk, which can come from the rolloff of the nearest neighbours or from the sidelobes of other channels
- Intra-band ripple, or transmission variations within a pass band
- 3dB bandwidth, which is the width of the passband
- Uniformity between passbands
- Channel Registration, or the accuracy with which the passband fits the targeted frequency/wavelength.
A design example
A DEMUX with the following high-level specs:
- C-band (1530 - 1561 nm) AWG
- Number of channels: 8
- channel spacing: 200 GHz
- FSR: 2000 GHz
- center frequency: 193.4 THz
- aperture core width: 2.0 um
The AWG designer combines physical simulation by CAMFR, the IPKISS modal solver, mathematical formulas and circuit simulation by CAPHE, the IPKISS circuit simulator to calculate parameters such as:
- number of arms
- grating circle
- aperture spacing
- waveguide lengths
Simulation results show that an improvement of the insertion-loss uniformity and the channel bandwidth are out of spec. Next we show how to improve these using the available tools from the Filter Toolbox:
A possible strategy to improve the insertion-loss uniformity: Increase the FSR
Increasing the FSR from 2000GHz to 3000GHz brings insertion loss difference down from 1.16dB to 0.49dB. The result is that the AWG's
- number of arms is up from 37 to 56
- the footprint is up 40% from 160,000 µm2 -> 218,000 µm2
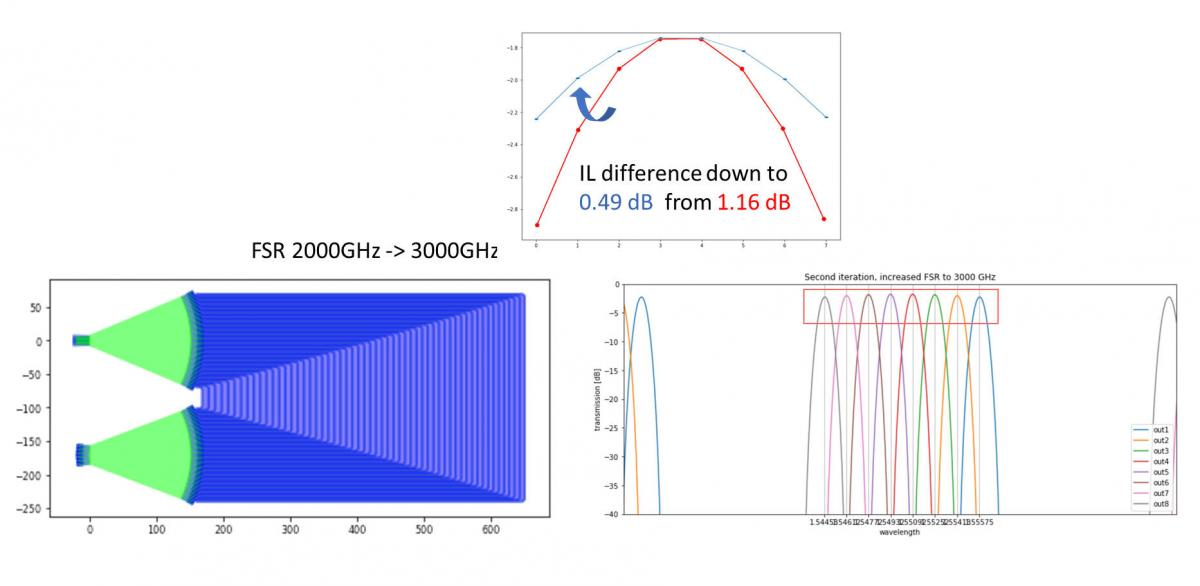
To increase the channel bandwidth, explore the type and shape of the apertures
A first strategy is to use an MMI aperture. We have used CAMFR, the IPKISS modal solver, to establish the optimal length of this device and thus an optimal field profile.
This has
- increased the channel bandwidth
- increased the insertion loss by 3dB
How to design a Arrayed waveguide grating (AWG) demultiplexer
Example on Luceda Academy